
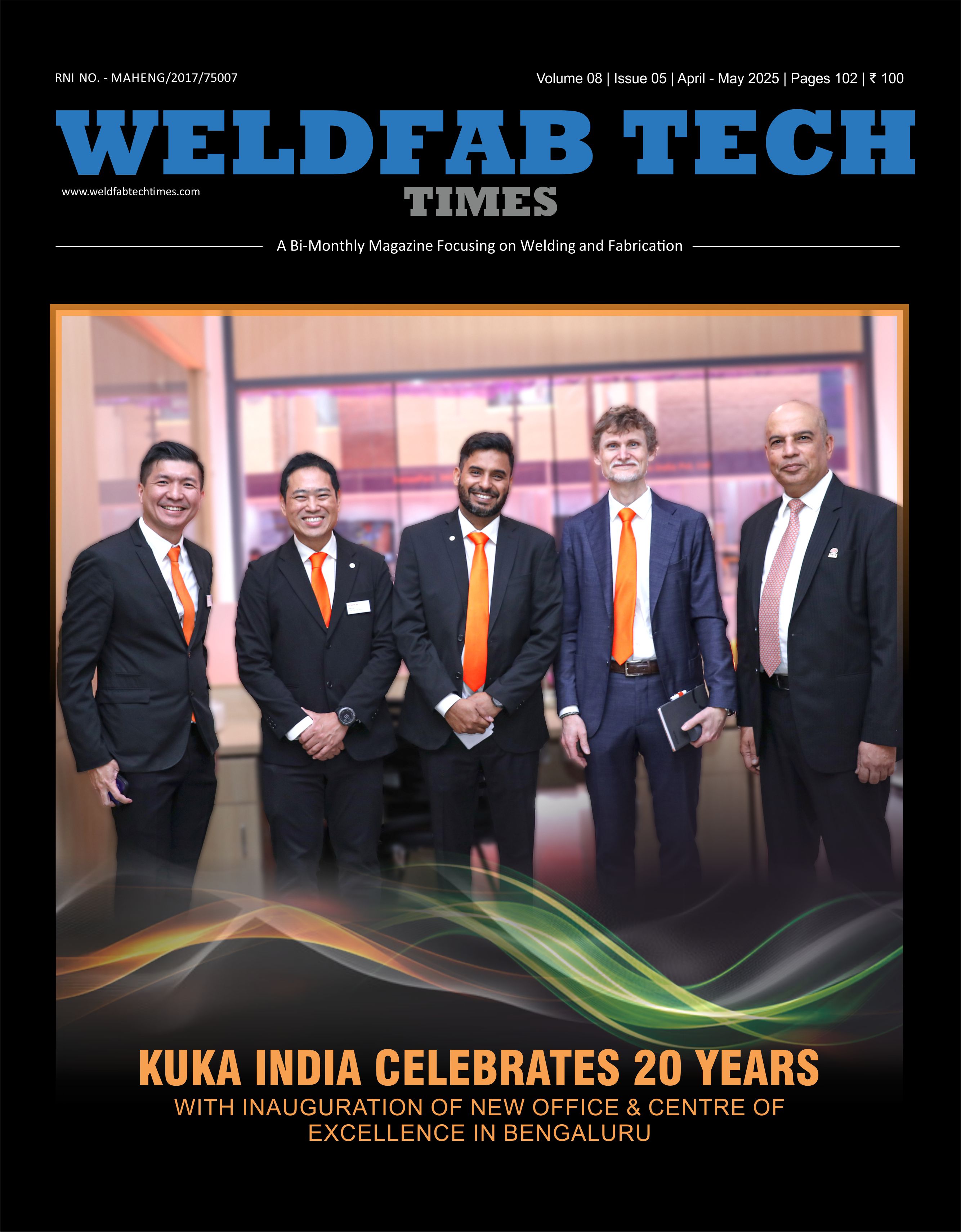
Latest Post
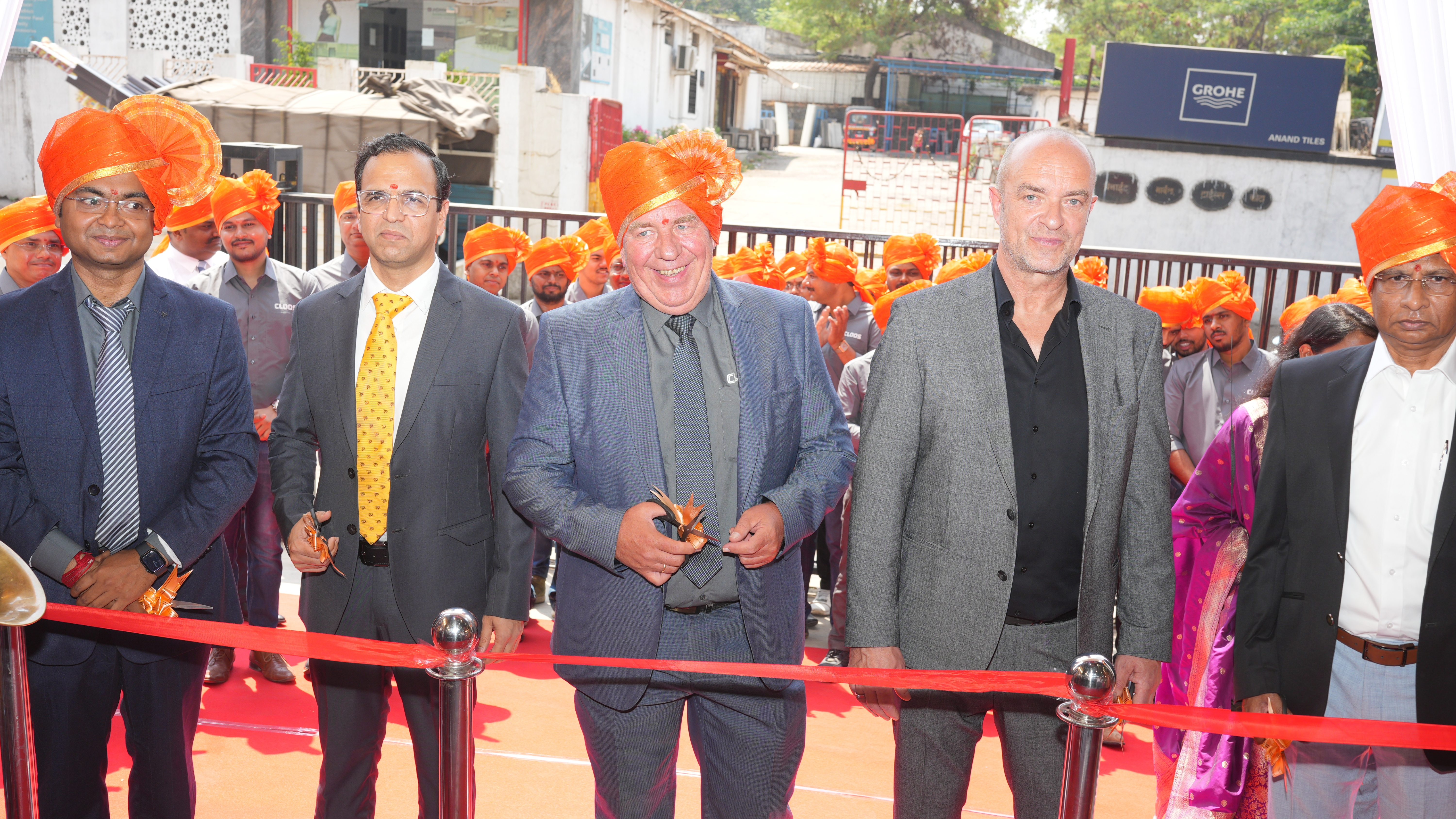
CLOOS India Inaugurates State-of-the-Art Experience Centre in Pune
2025-06-09

Pushing Boundaries in NDT An Interview with AWS International Agent, Advanced Technology Group
2025-06-09
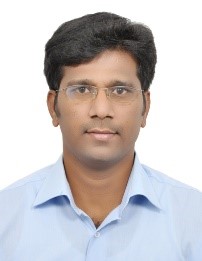
Challenges in qualifiying welding procedures for superduplex steel S32760
2025-06-09
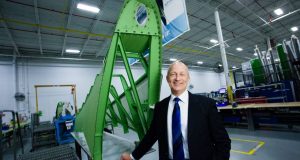
CPI Aerostructures completes acquisition of Welding Metallurgy Inc
2025-05-15

Pushing Boundaries in NDT An Interview with AWS International Agent, Advanced Technology Group
2025-06-09
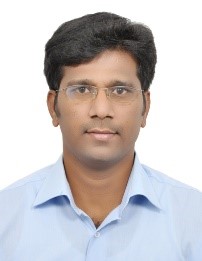
Challenges in qualifiying welding procedures for superduplex steel S32760
2025-06-09
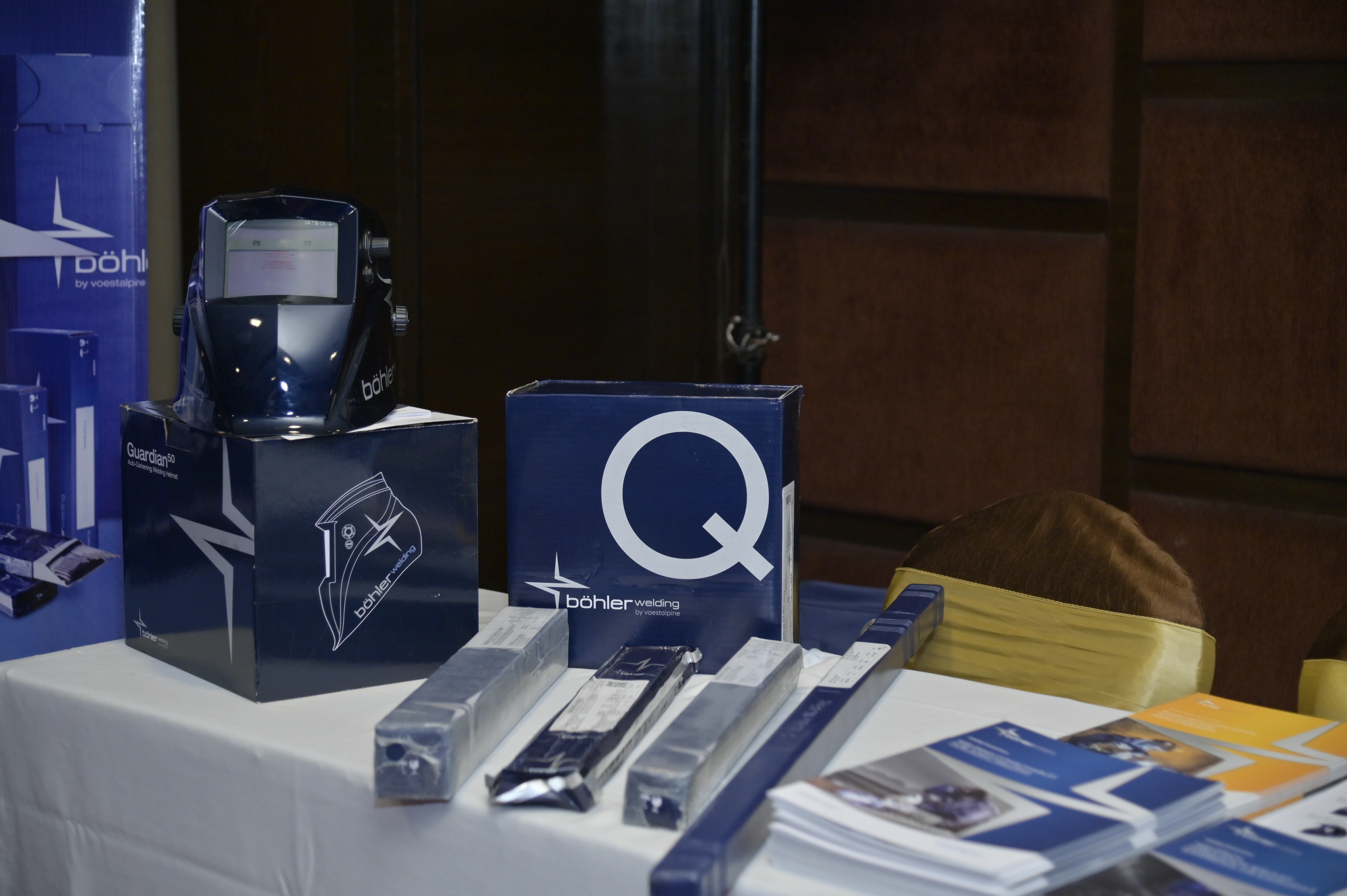
Effect of shielding gas composition on Ferrite Number, Mechanical & Microstructural Properties of GTAW deposited Austenitic Stainless Steel weld metal
2025-03-04
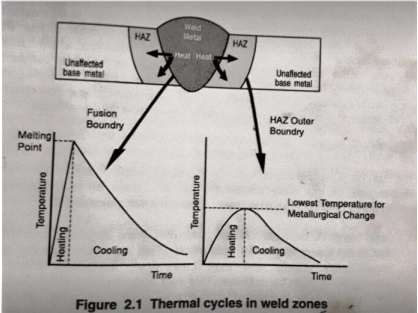
Heat Treatment
2025-05-22
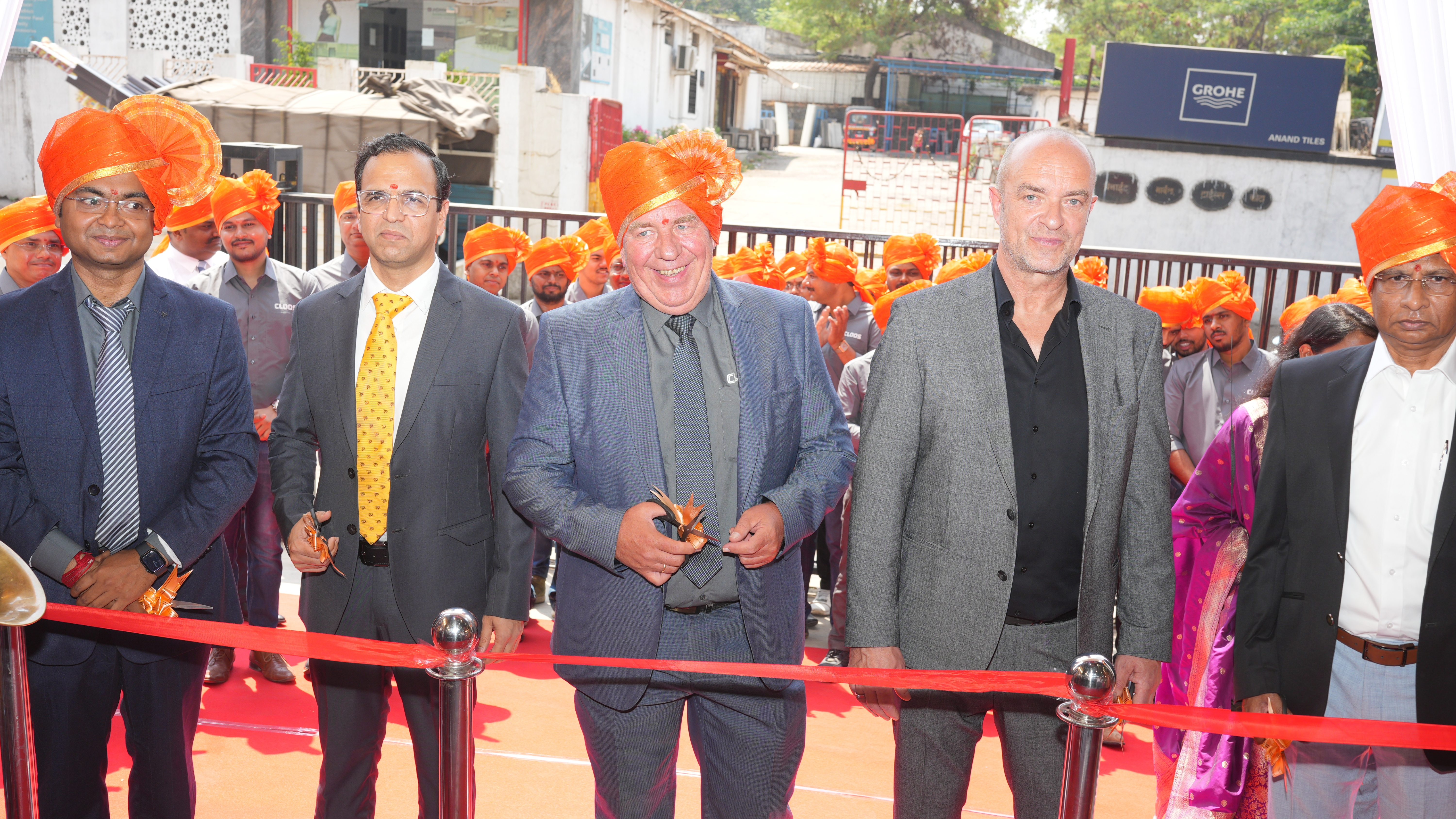
CLOOS India Inaugurates State-of-the-Art Experience Centre in Pune
2025-06-09
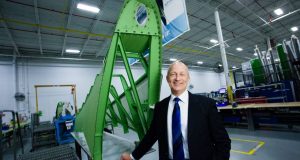
CPI Aerostructures completes acquisition of Welding Metallurgy Inc
2025-05-15
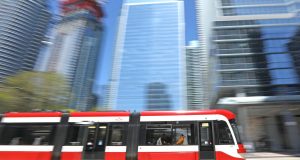
Most new TTC streetcars to be recalled to fix welding defect
2025-05-15
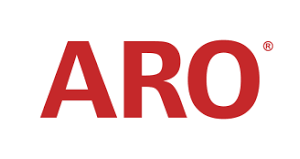
ARO Launches New Products in the EXP Diaphragm Pump Series at ChemTech 2019
2025-05-06
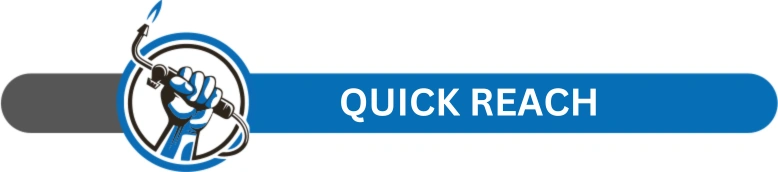
Get in touch with us quickly and easily—we’re here to help!
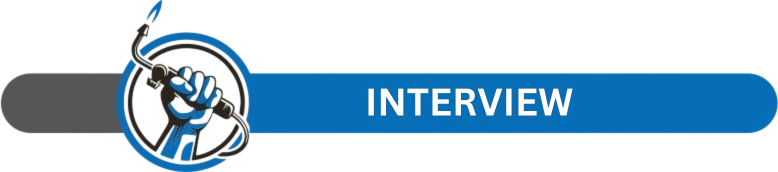
Dive into an exclusive interview with an industry expert.
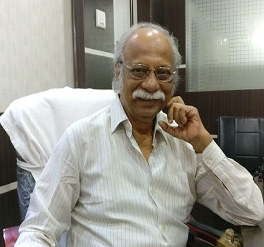
FIIW, FIE, MSNT, MAE, MITD
SHIELDING GAS SELECTION FOR GAS METAL ARC WELDING
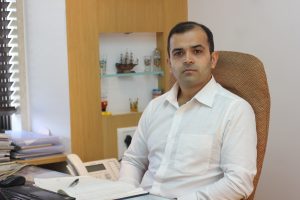
Director, Jayesh Group
“We are a One-Stop-Shop for Welding Industry offering all types of Ferro Alloy Powders, Metal Powders, Minerals, Chemicals and Steel Strips.”
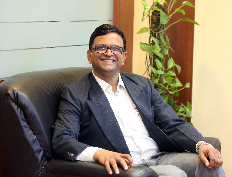
Executive Vice President and Business Head, Godrej Process Equipment
“Our welding engineering has over 1,900 qualified procedures.”
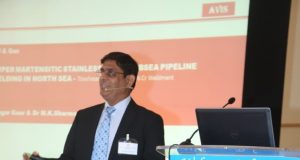
AequitasVeritas Industrial Services, Oslo/Vadodara
Welding in Subsea Project-Inconel 625 Cladding over C-Steel Forging
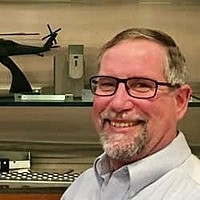
Cofounder of All-Type Welding and Fabrication
The most common stainless steel welding methods
.png)
A consultant to Welding Consumables & Fabrication industries, A Fellow of the Indian Welding Society, A Founder Chairman of IWS-Western Zone
S Sankaran : A consultant to Welding Consumables & Fabrication industries
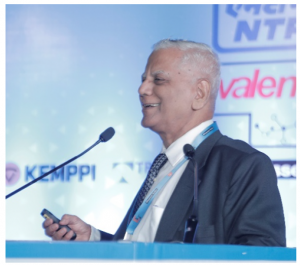
Managing Director, Weldwell Speciality Pvt. Ltd. Nivek Agencies
C. C. Girotra, Managing Director, Weldwell Speciality Pvt. Ltd.
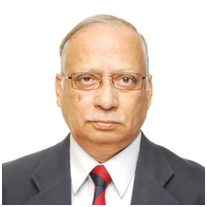
President vis-à-vis Chairman, International Committee of The Indian Institute of Welding (IIW-India)
Obituary: Parimal Biswas (16.04.1950 – 30.04.2021)
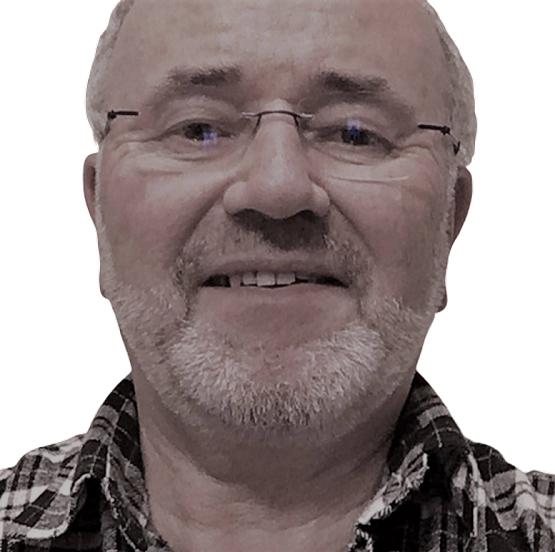
Sr. Welding Engineer (IWE) – Sr. Metallurgist (Civ.Eng),
Auxiliary Gas Shield: A bright idea – a bright weld
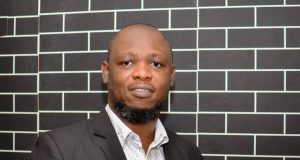
Chief Executive Officer, Nigerian Institute of Welding
Aryo Ardeniyi, Chief Executive Officer, Nigerian Institute of Welding
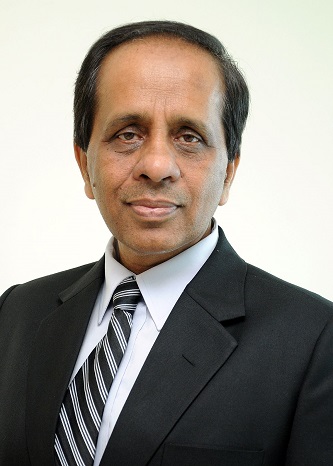
Business Consultant, WeldWell Speciality Pvt. Ltd
Thermal Spray Process – A Wear Combating Solution
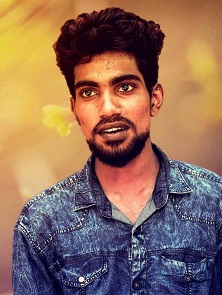
Welder
My biggest strength is my work
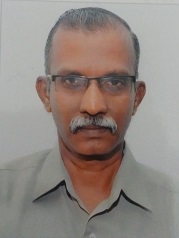
Former AGM BHEL, Tiruchirappalli, India
Welding and Post Weld Heat Treatment of WB 36 Steel
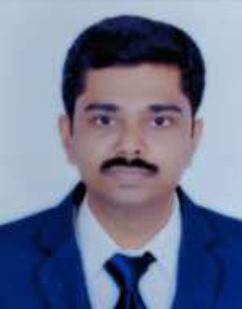
Senior DGM – MRU-QC &Welding, Larsen & Toubro Limited, Heavy Engineering IC
“Welding is an ever-growing discipline which presents challenges and work opportunities for new generations of engineers.”
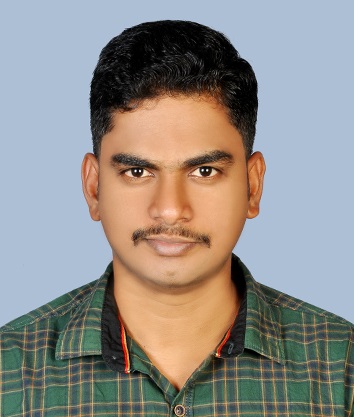
M.E (Welding Tech), Welding Engineer, Velmurugan Heavy Engg. Industries, Tamilnadu
“I spell welding in three stages before, during, after welding. It helps to avoid mistakes.”
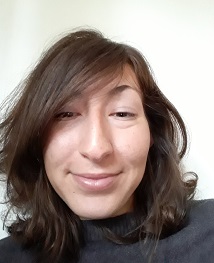
CEO, The Welding Workshop AWS Certified Welder
Women in Welding, : “I aim to always learn and grow as a welder and educator”
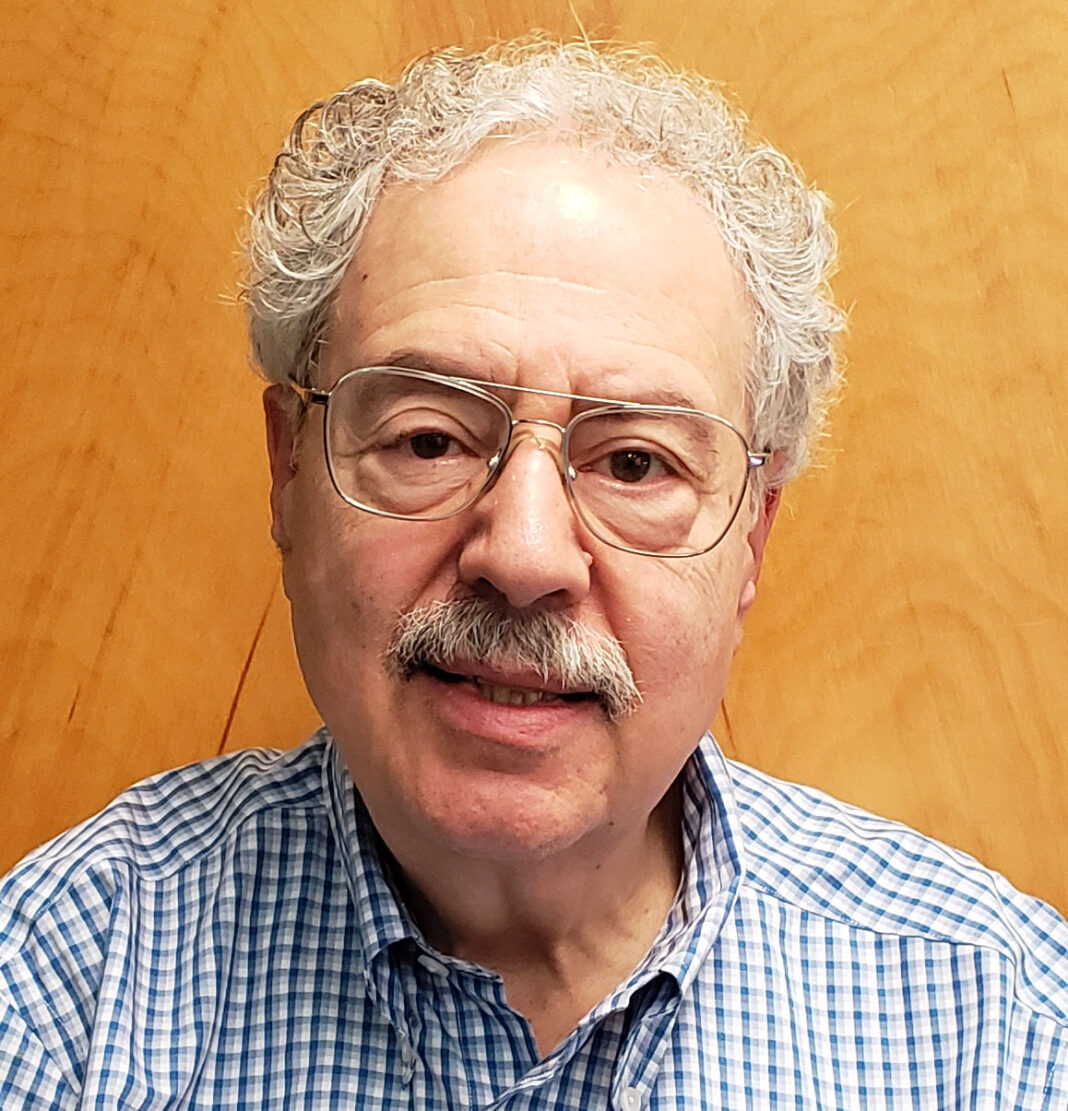
President of Unitrol Electronics Inc. of Northbrook, Illinois, and former chair of the Resistance Welding Manufacturing Alliance (RWMA), a standing subcommittee of the AWS.
Making your Spot Welder Safer
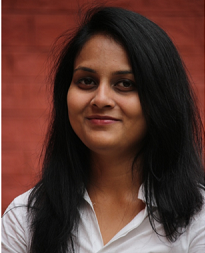
Welding Engineer, Inox India Pvt Ltd.
Welding is not an exception…
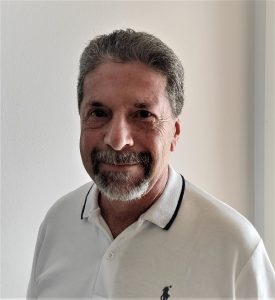
Visiting Professor, University West, Sweden, A Welding Technology Consultant
Prof. Américo Scotti, Visiting Professor, University West, Sweden
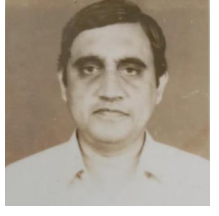
Senior General Manager(Welding)
V.S. Galgali
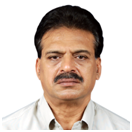
Head CoEW, PSG college of Technology, Coimbatore (Former Head of WRI, BHEL Tiruchirappalli)
Centre Of Excellence In Welding (COEW)
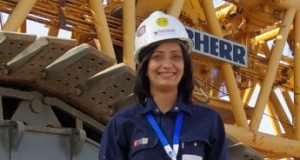
Samar Emara, Welding and piping Inspector at TechnipFMC, Egypt
Samar Emara, Welding and piping Inspector at TechnipFMC, Egypt
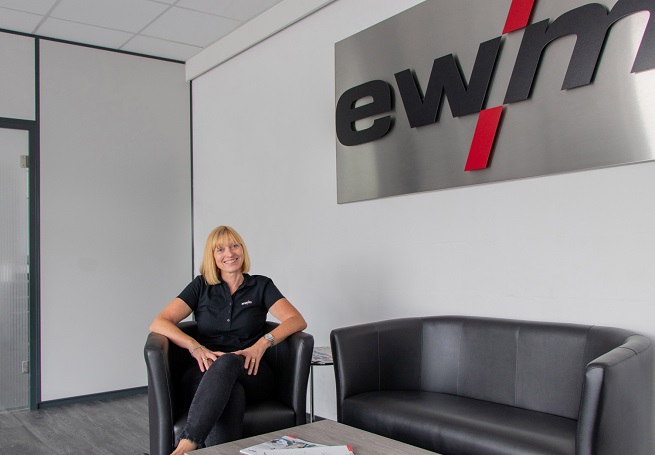
The first female president of the German Welding Society President of the Koblenz Chamber of Industry and Commerce Chairperson of the Supervisory Board of EWM AG
Susanne Szczesny-Oßin
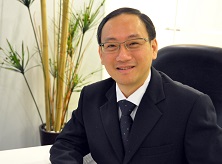
Head of Marketing (Asia Pacific), FARO Technologies
FARO’s portfolio of 3D measurement provides turnkey solutions for manual and automated inspection and analysis.
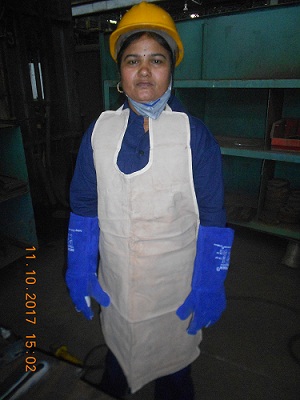
Technician-III, Trade- Welder Shop- Welding Shop
Woman Welder at Parel Workshop: A snapshot
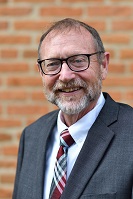
Manager of Welding Engineering, Vermeer Corporation President (2020-2023), International Institute of Welding Past President (2015)
We need to train people to weld more like robots and teach robots to weld more like people.
.jpg)
Altec Expert – W&C (Middle East & India)
New developments in gas shielded arc welding of aluminium alloys using gas mixtures containing minor gaseous
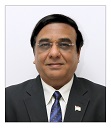
Executive Vice President, Jindal Steel & Power Ltd.
Head Hardened Rails
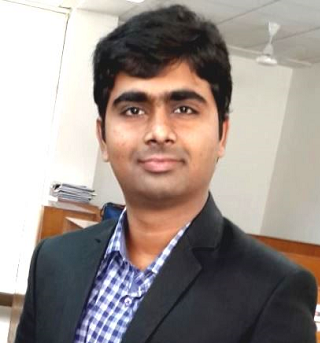
Department of Mechanical Engineering
An experimental approach on friction stir welding process parameters and tool design for dissimilar joints
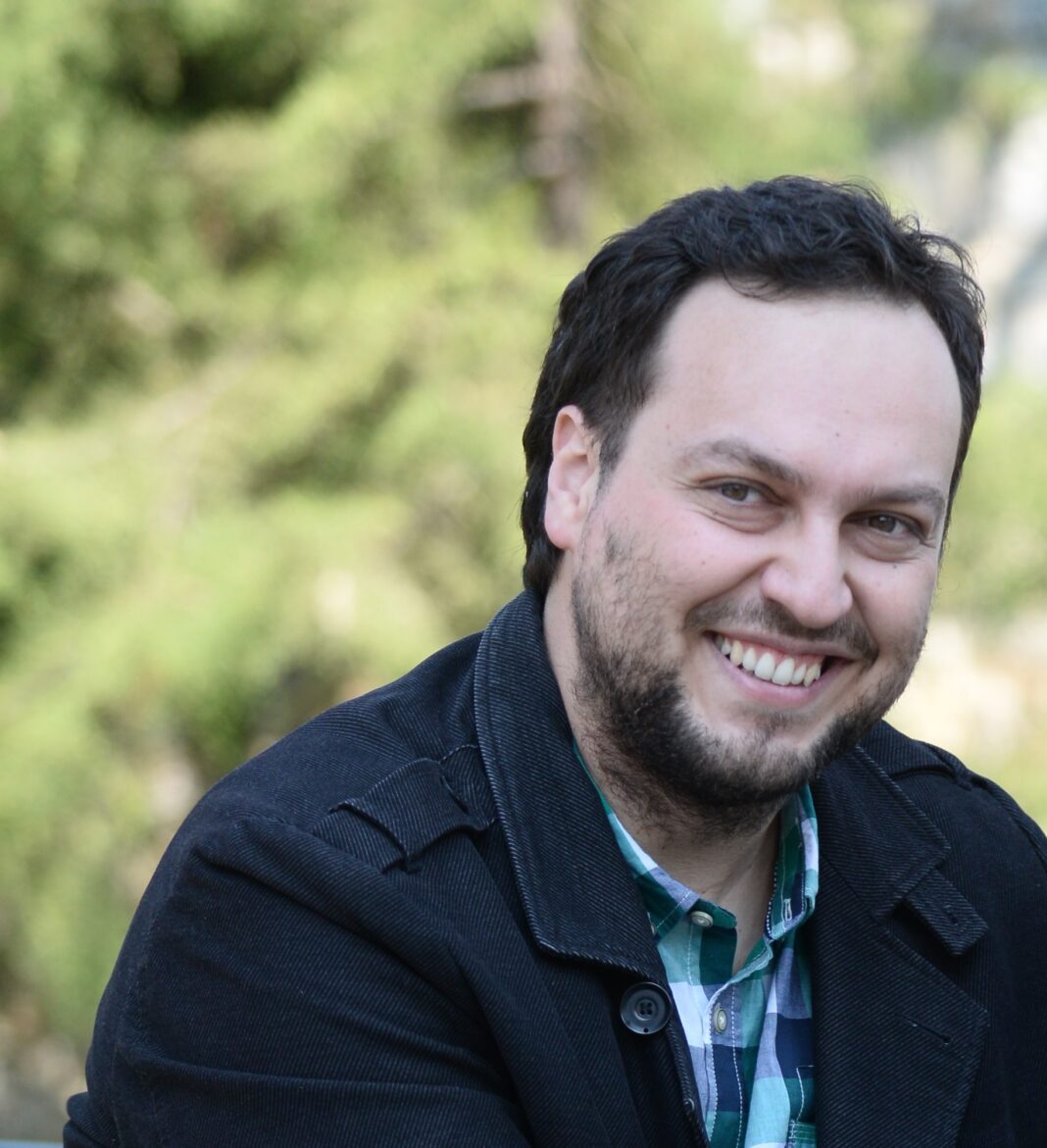
Mechanical Engineering, IWE Welding engineering specialist
I always prefer working as per the given standards, and I’m sure, this is the right way to complete any project.
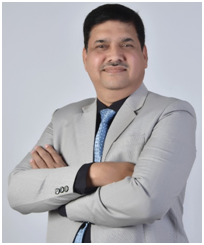
CEO – INOX India Pvt. Ltd.
We installed Liquid Medical Oxygen tanks in more than 250+ hospitals all over India and our Parent Company supplied liquid medical oxygen to more than 1000+ hospitals.
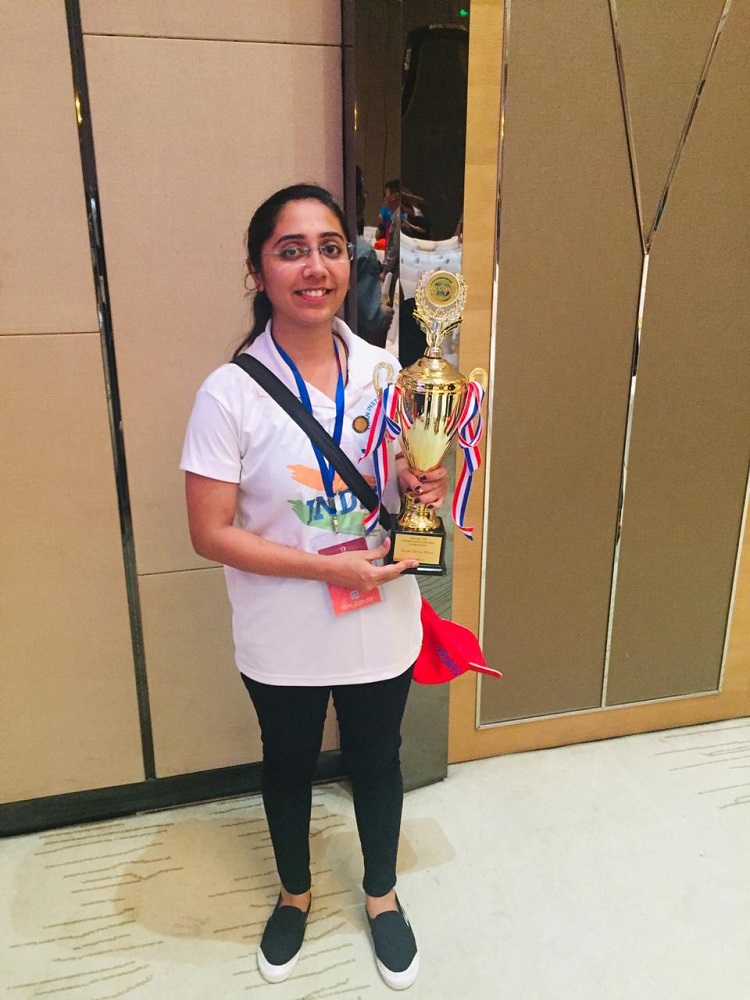
Contractual Employee, Welder, Mahindra Vehicles Manufacturers Ltd.
I want to represent my country at the highest level of welding competitions
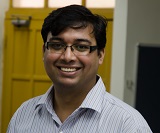
Sigma Weld, EDWPL
Increased Productivity in GTAW
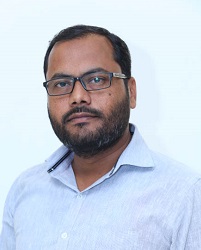
International Expert – W&C (ALTEC – Middle East & India), Air Liquide India
Ways to reduce Spatter generations
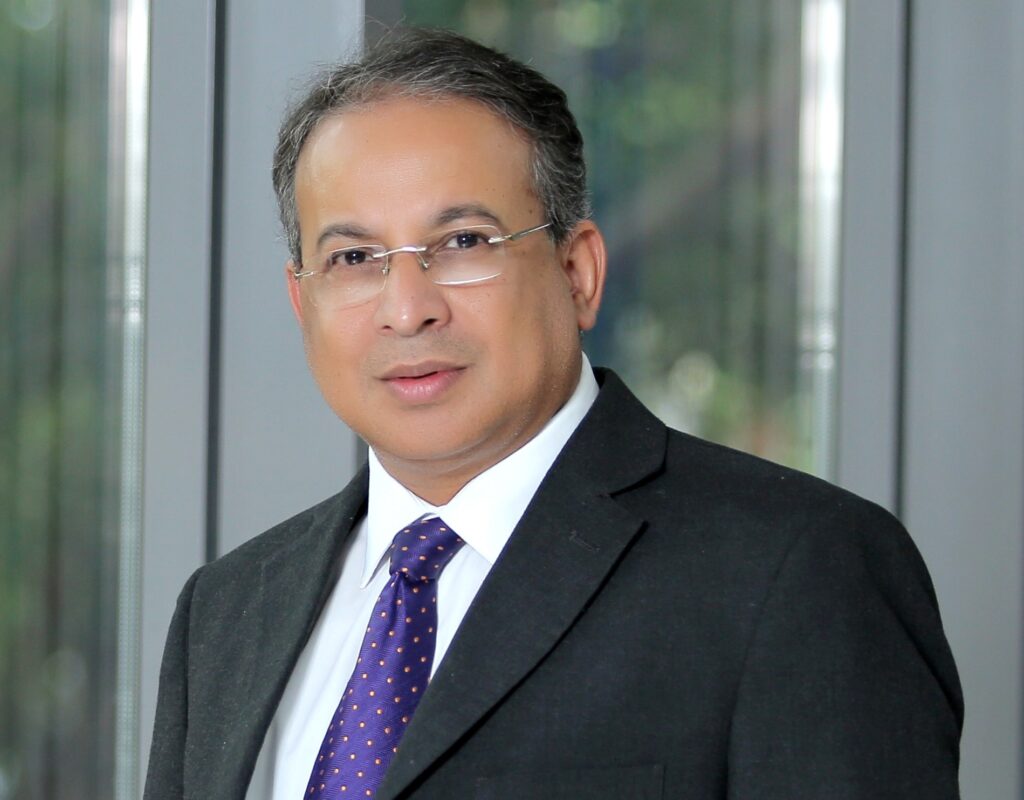
CEO & Managing Director, Tata Power
Welding and welding skills will continue to grow in demand.
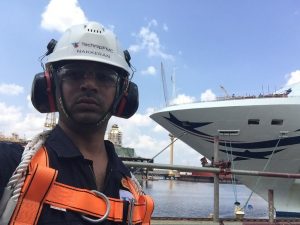
Welding Engineer (IWE/EWE)
Nakkeran T, Welding Engineer (IWE/EWE)
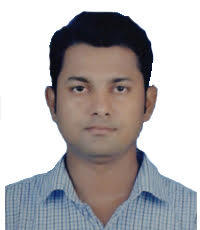
Welder Trade, Mazagaon Dock
Sagar D. Shilimkar, Welder Trade, Mazagaon Dock
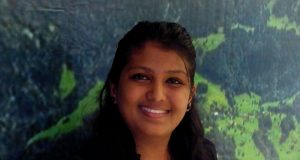
Publisher, Weldfab Tech Times Magazine
Welding World By Eliza Bhalerao, Publisher, Weldfab Tech Times Magazine
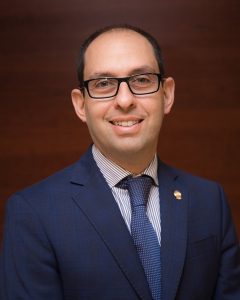
Chief Executive Officer
Luca Costa, Chief Executive Officer, IIW
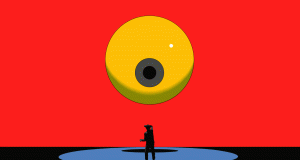
Project Manager, Al Fajer Information & Services
TEKNO 2017: An excellent opportunity to comprehend technical aspects of the industry.
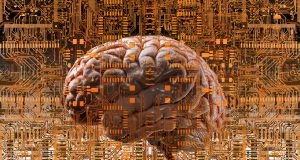
Managing Director, Fronius India Private Limited.
We have machines that are a perfect blend between the man and machines.
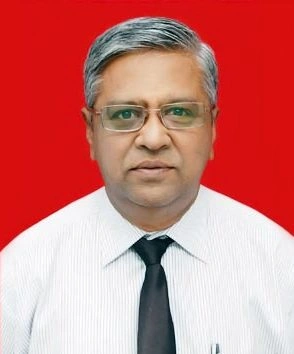
President, Indian Institute of Welding (IIW)
There is a huge market for welding in India.
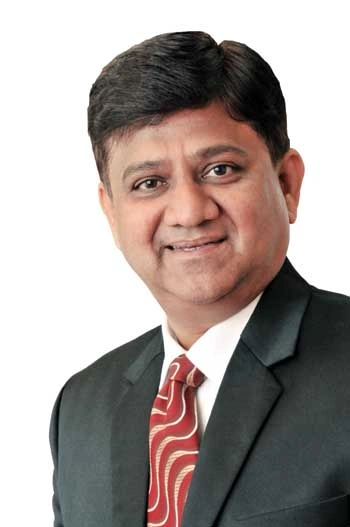
Managing Director, Ador Welding Ltd (AWL)
Welding Automation Division is an important cog in our wheel towards furthering our growth.
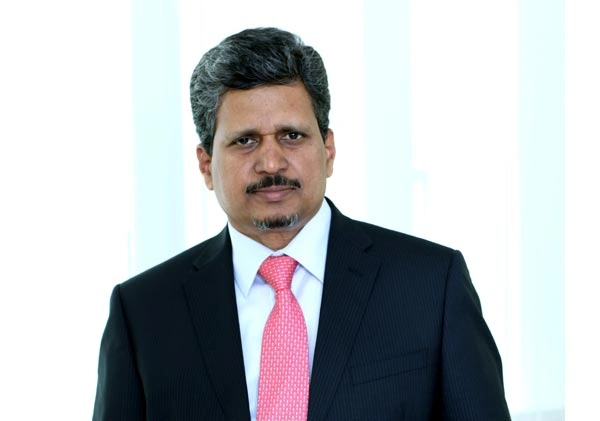
Director General & CEO, Indian Machine Tool Manufacturers’ Association (IMTMA)
The machine tool industry is a key to ‘Make in India’
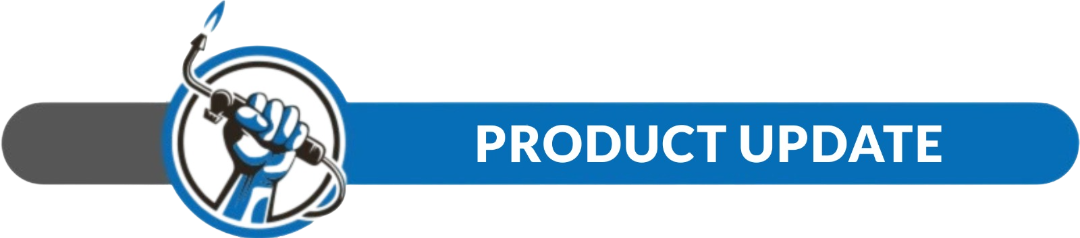
Explore Latest Welding Products