Challenges in qualifiying welding procedures for superduplex steel S32760
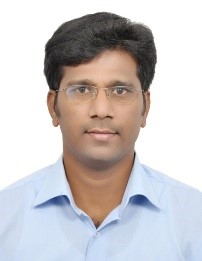
During the engineering
stage, the organization had selected SDSS S32760 material as MOC
(Vessel thickness is 10mm) based on their design basis (Sour
service). The organization has qualified welding procedures
with various parameters but could not pass the corrosion testing
of the ASTM A 923 method C. Upon investigation, it
was found that a lack of experience
personnel w.r.t. selected material was the prime reason for
the failures of PQR corrosion testing.
Based on general
practises of exotic materials, initially trials were carried out with shielding
gas of 99.999% Argon, interpass of 90°C and heat input 1.55KJ/mm. Corrosion
properties inline with A 923 method were not met and not even closer to
acceptance range (10mdd at test temp 40° c).Procured materials like pipe,
flange & cap end were supplied in
solution annealed condition and were corrosion requirements.International
consumable manufactures have been consulted to guarantee the corrosion
properties for S32760, unfortunately none of them provided the guarantee.
Testing and Analysis
Girth welds must be of the welding process GTAW manual and are one
of the bottlenecks of fabrication.About 10 trails were carried
and tested for mechanical, chemical (including PREN) and corrosion
properties. Ferrite count (35-60%) were tested in accordance with ASTM E
562 along with metallography study for any intermetallic precipitates. Below
various combinations were part of the trials and modified to stringent
requirements to meet the corrosion criteria.
·
Increase of travel speed especially for root & coldpass
·
Change of shielding & backing gas from Argon to Ar+2% N2
·
Interpass temperature from 90° C to 50°c
·
Restricting heat input for Root and coldpass
·
Highest cleaning practices in handling base material,
consumable and fabrication tools
At last, best practices
of super duplex were implemented in order to meet the corrosion
criteria. Even after that, organization has found that the corrosion
results were not consistent with the trails. One of the NACE article
(paper 8838) has clearly states that it is difficult for SDSS to pass corrosion
test of A 923 method C and is not repeatable.
All purchased welded
pipes of S32760 were meeting the corrosion requirements of A 923 method
C. On comparing,we found that that the rootcause for the failures.
• Process used for welded pipes were mechanized process, whereas
organziation had utilized manual GTAW process.Travel speed was higher in case
of welded pipes than the manual welding process
• The welded pipes were undergone solution annealing heat
treatment, whereas girth weld had not undergone any heat treatment.
The root pass is difficult to be welded with
travel speed of 65 mm minimum by a manual
craftmen. Compared to SS 316L, fluidity of weld pool is less for SDSS materials. Base material is difficult to fuse. More over minimum 65 mm travel speed, the welders were not able to fuse base materials properly, resulted in lack of fusion and undercut defects. Organization has put tremendous effort to train to achieve the travel speed during vessel fabrication. However, organization has selected S32750 Grade and were able to meet all chemical, mechanical, ferrite and corrosion requirements, while following general practices of exotic requirements as shown below
· Travel speed of 45mm/min for rootpass
· Shielding & backing gas Ar+2% N2
· Interpass temperature 100° C
· Heat input for Root (0.6-1.2 kj/mm) and coldpass (0.5-0.9 Kj/mm)
· Filler metal of 1.6,2.0 & 2.4 mm
Conclusion:
S32760 may not be recommended for the fabrication to suit this corrosion requirement, whereas S32750 would be ideal to meet both fabrication and technical requirements. Many recommend accepting S32760 grade with a corrosion requirement inline with an international standard ISO 17781. Acceptance criteria is 4.0g/m2 at test temperature of 35°c which is less stringent than A 923 method C.
Recommendations
Corrosion criteria can be achieved ,if Grade S32760 meets below recommendations during welding procedure qualification.
1. Travel speed to be maintained 65 mm/minute minimum in root pass welding
2. Travel speed cold pass should be higher than the root pass. The value may range from 100-125mm
3. Shielding and backing gas Ar+2%N2 would be the best
4. Interpass to 50°C is highly recommended due to low thickness
5. Oxygen content limit to 500 ppm during back purging
6. Heat input shall be limited to 0.6-0.9 Kj/mm and cold pass to 0.52-0.86 Kj/mm
7. Filler metal shall be 2.0 mm dia for Root and 2.4 for cold, fill & cap passes
8. Competent craftmen shall be utilized
9. Control of repairs such as Lack of fusion and undercut due to higher travel speed of 65mm/Min minimum
References
ASTM A 923: Standard Test Methods for Detecting Detrimental Intermetallic Phase in Duplex Austenitic/Ferritic Stainless Steels
ISO 17741 : Petroleum, petrochemical and natural gas industries — Test methods for quality control of microstructure of ferritic/austenitic (duplex) stainless steels
NACE Article: The Validity of Using the ASTM A923 Test Method C Corrosion Test for Weld Procedure Qualification of 25% Chrome Duplex Stainless Steels
ASTM E 562: Standard Test Method for Determining Volume Fraction by Systematic Manual Point Count.
Keep Up to Date
with the Most
Important News
By clicking the Subscribe button, you confirm that you have read and are agreeing to our Privacy Policy and Terms of Use.
Add a Comment
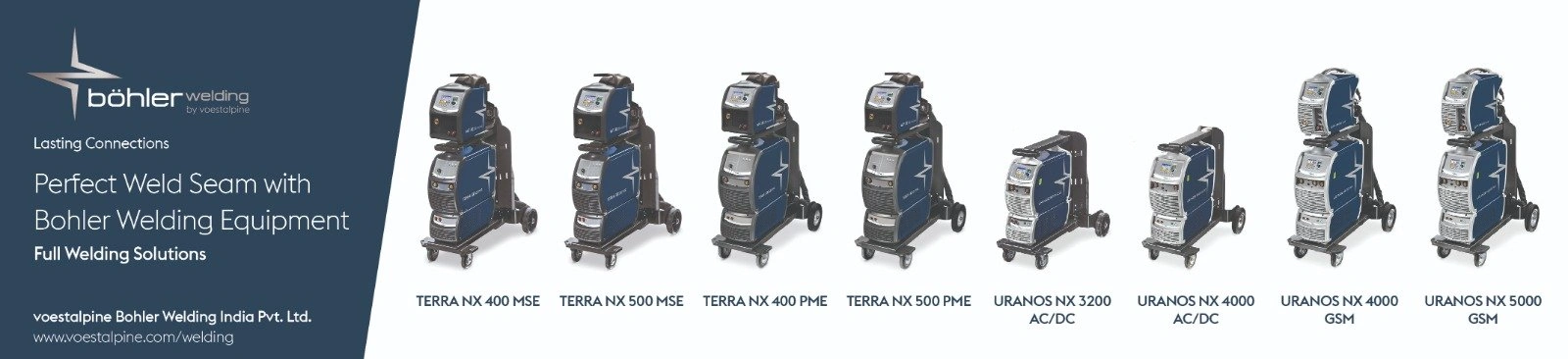
Recommended for You
During the engineering
stage, the organization had selected SDSS S32760 material as MOC
(Vessel thickness is 10mm) based on their design basis (Sour
service). The organization has qualified welding procedures
with various parameters but could not pass the corrosion testing
of the ASTM A 923 method C. Upon investigation, it
was found that a lack of experience
personnel w.r.t. selected material was the prime reason for
the failures of PQR corrosion testing.
Based on general
practises of exotic materials, initially trials were carried out with shielding
gas of 99.999% Argon, interpass of 90°C and heat input 1.55KJ/mm. Corrosion
properties inline with A 923 method were not met and not even closer to
acceptance range (10mdd at test temp 40° c).Procured materials like pipe,
flange & cap end were supplied in
solution annealed condition and were corrosion requirements.International
consumable manufactures have been consulted to guarantee the corrosion
properties for S32760, unfortunately none of them provided the guarantee.
Testing and Analysis
Girth welds must be of the welding process GTAW manual and are one
of the bottlenecks of fabrication.About 10 trails were carried
and tested for mechanical, chemical (including PREN) and corrosion
properties. Ferrite count (35-60%) were tested in accordance with ASTM E
562 along with metallography study for any intermetallic precipitates. Below
various combinations were part of the trials and modified to stringent
requirements to meet the corrosion criteria.
·
Increase of travel speed especially for root & coldpass
·
Change of shielding & backing gas from Argon to Ar+2% N2
·
Interpass temperature from 90° C to 50°c
·
Restricting heat input for Root and coldpass
·
Highest cleaning practices in handling base material,
consumable and fabrication tools
At last, best practices
of super duplex were implemented in order to meet the corrosion
criteria. Even after that, organization has found that the corrosion
results were not consistent with the trails. One of the NACE article
(paper 8838) has clearly states that it is difficult for SDSS to pass corrosion
test of A 923 method C and is not repeatable.
All purchased welded
pipes of S32760 were meeting the corrosion requirements of A 923 method
C. On comparing,we found that that the rootcause for the failures.
• Process used for welded pipes were mechanized process, whereas
organziation had utilized manual GTAW process.Travel speed was higher in case
of welded pipes than the manual welding process
• The welded pipes were undergone solution annealing heat
treatment, whereas girth weld had not undergone any heat treatment.
The root pass is difficult to be welded with
travel speed of 65 mm minimum by a manual
craftmen. Compared to SS 316L, fluidity of weld pool is less for SDSS materials. Base material is difficult to fuse. More over minimum 65 mm travel speed, the welders were not able to fuse base materials properly, resulted in lack of fusion and undercut defects. Organization has put tremendous effort to train to achieve the travel speed during vessel fabrication. However, organization has selected S32750 Grade and were able to meet all chemical, mechanical, ferrite and corrosion requirements, while following general practices of exotic requirements as shown below
· Travel speed of 45mm/min for rootpass
· Shielding & backing gas Ar+2% N2
· Interpass temperature 100° C
· Heat input for Root (0.6-1.2 kj/mm) and coldpass (0.5-0.9 Kj/mm)
· Filler metal of 1.6,2.0 & 2.4 mm
Conclusion:
S32760 may not be recommended for the fabrication to suit this corrosion requirement, whereas S32750 would be ideal to meet both fabrication and technical requirements. Many recommend accepting S32760 grade with a corrosion requirement inline with an international standard ISO 17781. Acceptance criteria is 4.0g/m2 at test temperature of 35°c which is less stringent than A 923 method C.
Recommendations
Corrosion criteria can be achieved ,if Grade S32760 meets below recommendations during welding procedure qualification.
1. Travel speed to be maintained 65 mm/minute minimum in root pass welding
2. Travel speed cold pass should be higher than the root pass. The value may range from 100-125mm
3. Shielding and backing gas Ar+2%N2 would be the best
4. Interpass to 50°C is highly recommended due to low thickness
5. Oxygen content limit to 500 ppm during back purging
6. Heat input shall be limited to 0.6-0.9 Kj/mm and cold pass to 0.52-0.86 Kj/mm
7. Filler metal shall be 2.0 mm dia for Root and 2.4 for cold, fill & cap passes
8. Competent craftmen shall be utilized
9. Control of repairs such as Lack of fusion and undercut due to higher travel speed of 65mm/Min minimum
References
ASTM A 923: Standard Test Methods for Detecting Detrimental Intermetallic Phase in Duplex Austenitic/Ferritic Stainless Steels
ISO 17741 : Petroleum, petrochemical and natural gas industries — Test methods for quality control of microstructure of ferritic/austenitic (duplex) stainless steels
NACE Article: The Validity of Using the ASTM A923 Test Method C Corrosion Test for Weld Procedure Qualification of 25% Chrome Duplex Stainless Steels
ASTM E 562: Standard Test Method for Determining Volume Fraction by Systematic Manual Point Count.
Comments
No comments available.