
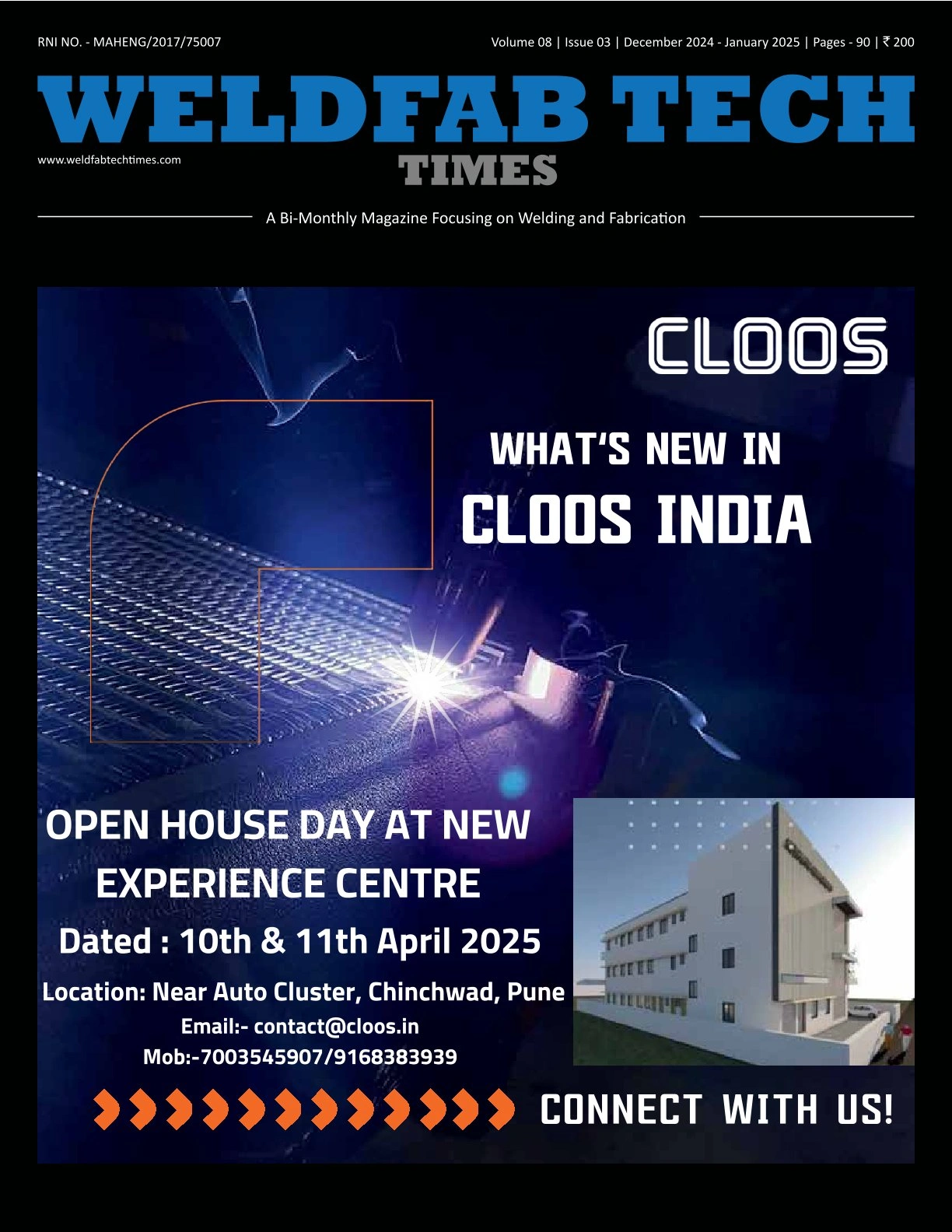
Latest Post
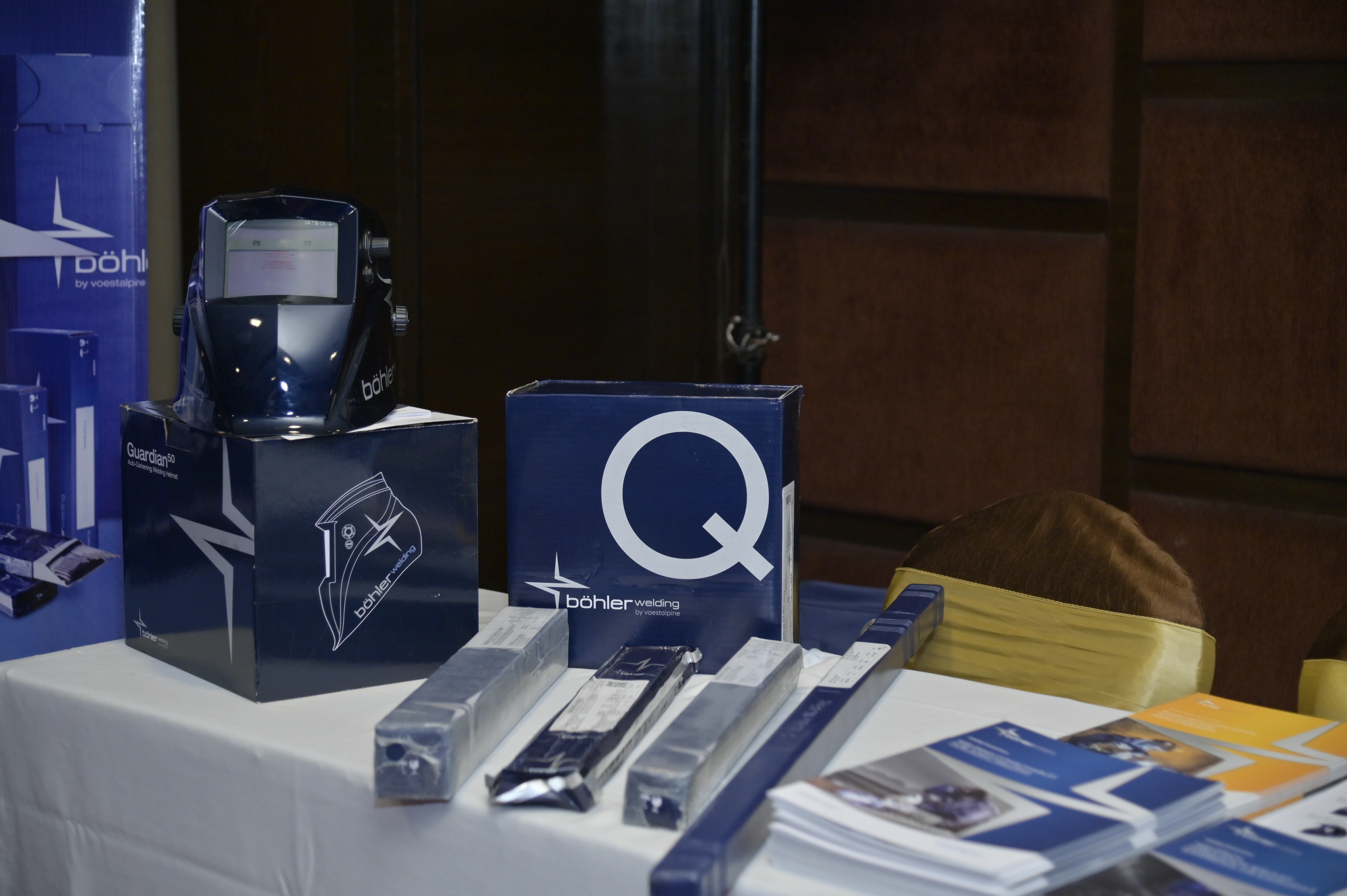
Effect of shielding gas composition on Ferrite Number, Mechanical & Microstructural Properties of GTAW deposited Austenitic Stainless Steel weld metal
2025-03-04
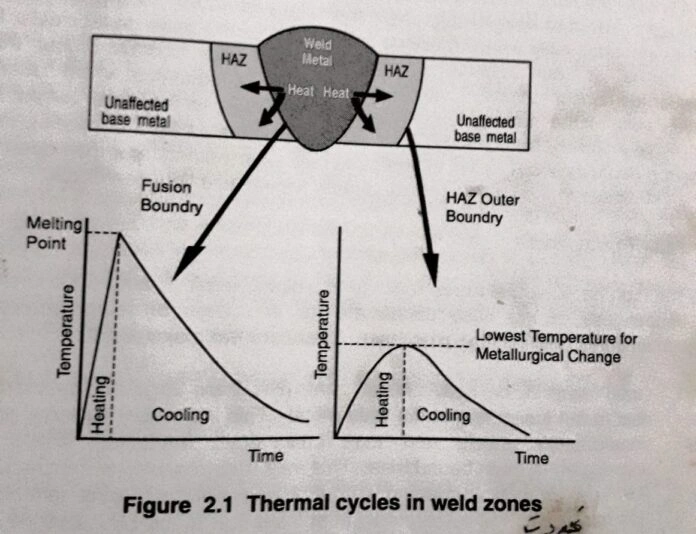
Heat Treatment
2025-01-16
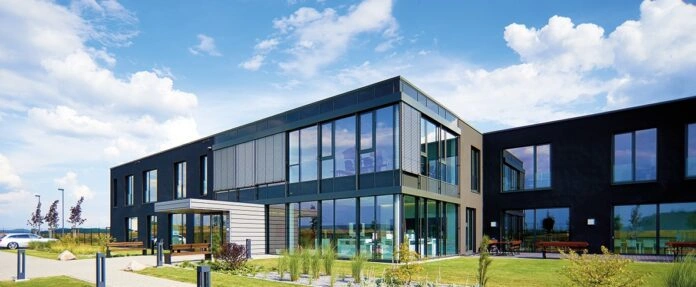
SKS Welding Systems: Pioneering Excellence in Welding Technology
2025-01-15
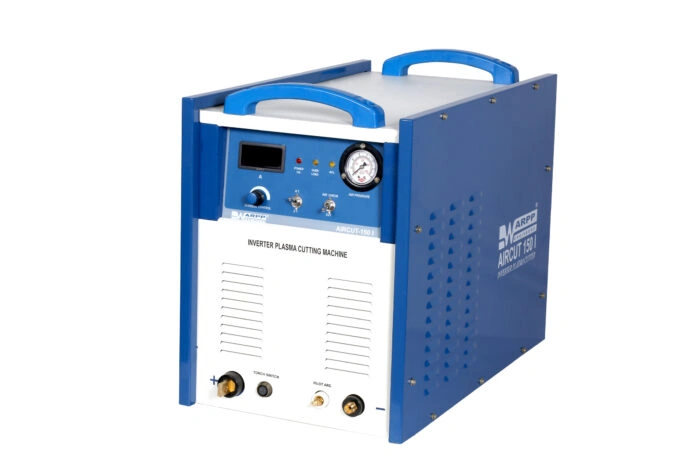
Inverter Based Air PlasmaCutting Machine
2025-01-15
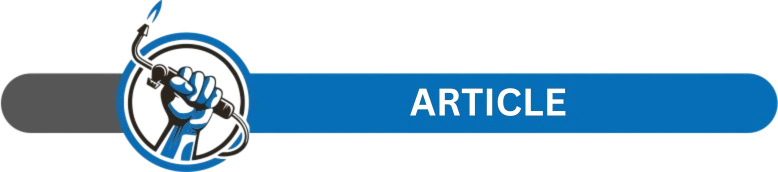
Explore Insightful Articles
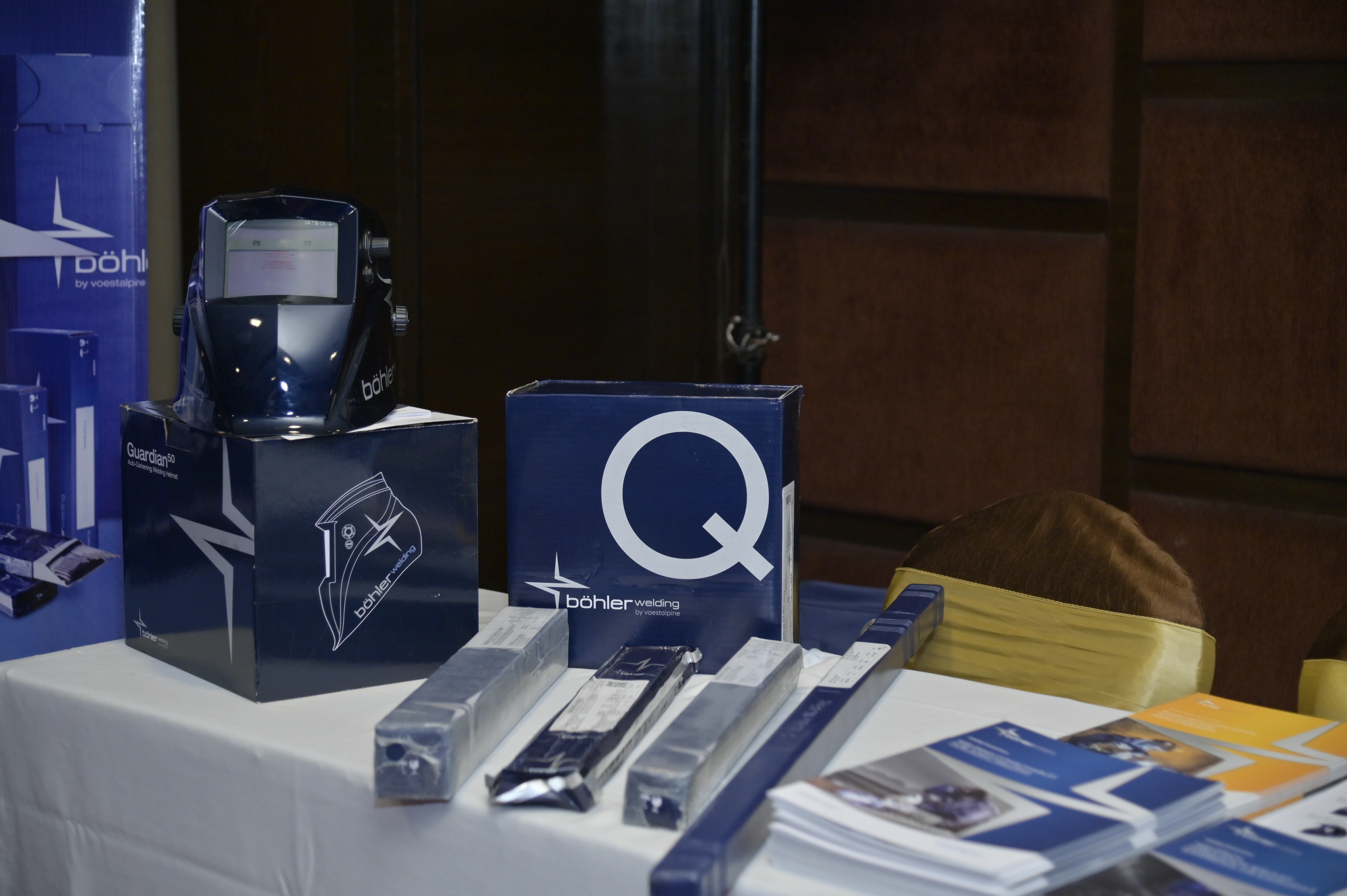
Effect of shielding gas composition on Ferrite Number, Mechanical & Microstructural Properties of GTAW deposited Austenitic Stainless Steel weld metal
2025-03-04
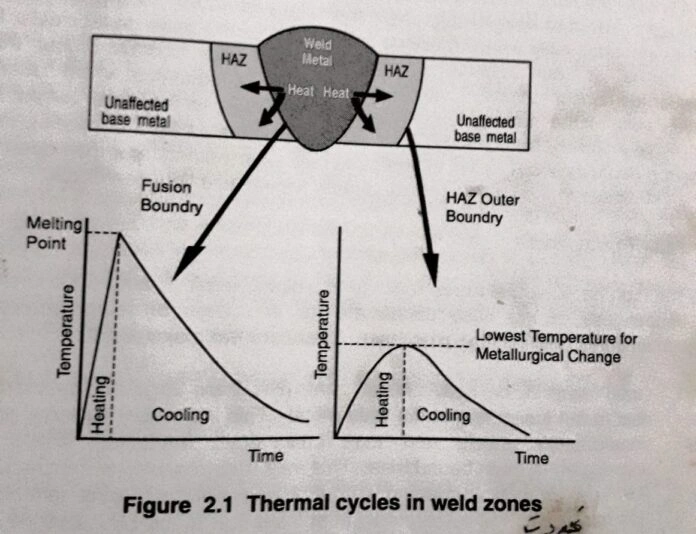
Heat Treatment
2025-01-16
.webp)
FABRICATING A SPLENDID GROWTH STORY FOR INDIA
2025-01-05
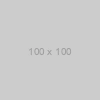
Advanced Joining Processes for Lightweight Electric Vehicles
2025-03-24
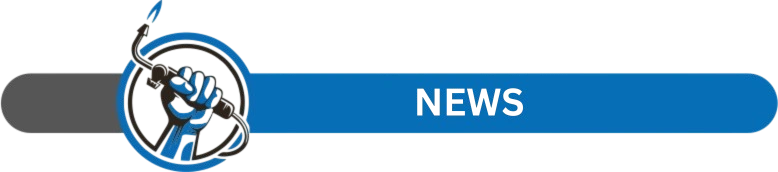
Explore Insightful News
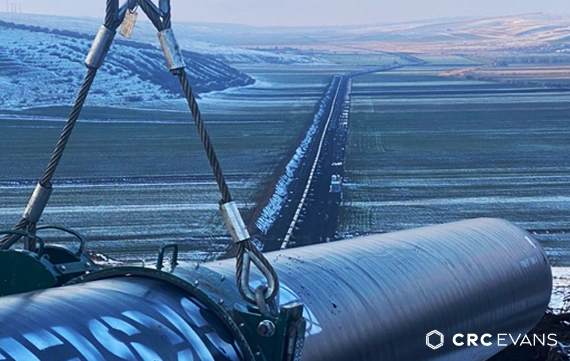
CRC Evans leads in hydrogen pipeline delivery
2025-01-15
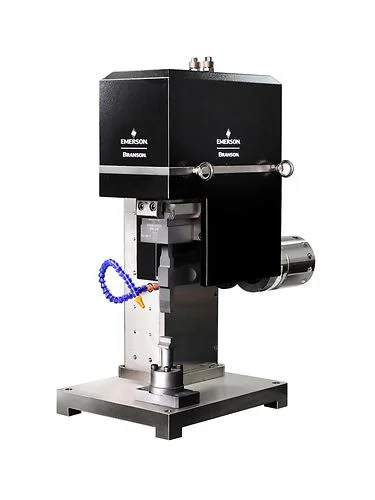
Emerson introduces Ultrasonic Metal Welders with Advanced Controls for Fast-Cycling, High-Precision Welds
2025-01-15
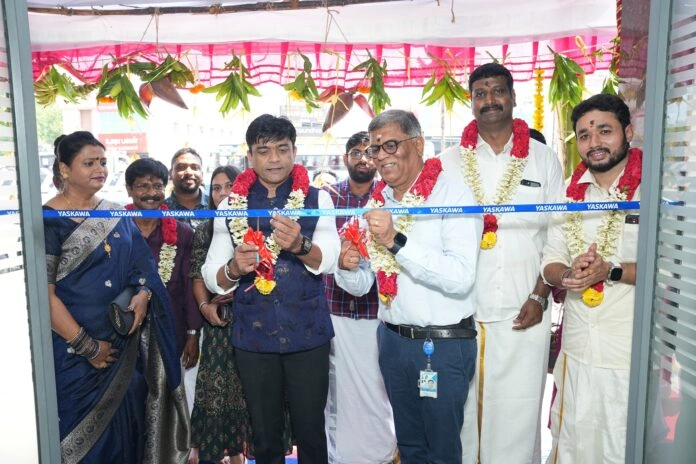
Celebrating a New Chapter: Yaskawa India’s Newly renovated Chennai Office Inauguration
2025-01-15
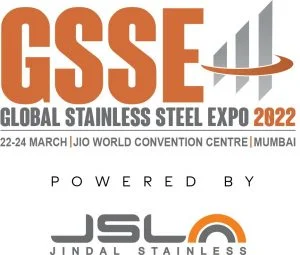
Welding and Fabrication specialists will ‘steel the show’ at GSSE 2022
2024-12-28
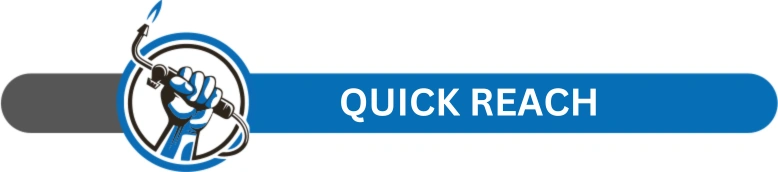
Get in touch with us quickly and easily—we’re here to help!
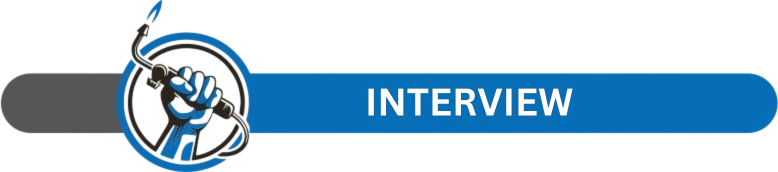
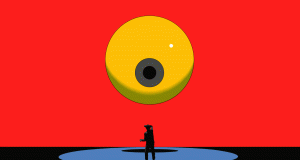
Project Manager, Al Fajer Information & Services
TEKNO 2017: An excellent opportunity to comprehend technical aspects of the industry.
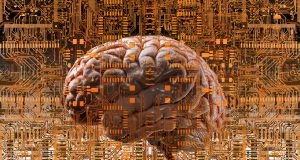
Managing Director, Fronius India Private Limited.
We have machines that are a perfect blend between the man and machines.
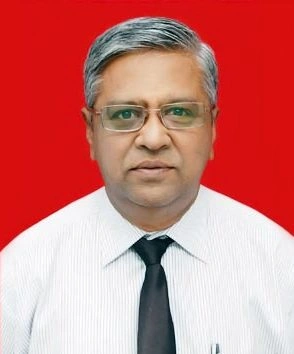
President, Indian Institute of Welding (IIW)
There is a huge market for welding in India.
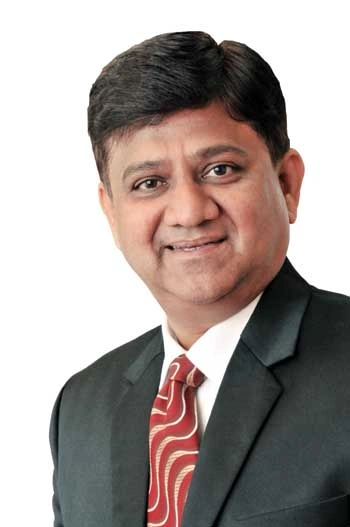
Managing Director, Ador Welding Ltd (AWL)
Welding Automation Division is an important cog in our wheel towards furthering our growth.
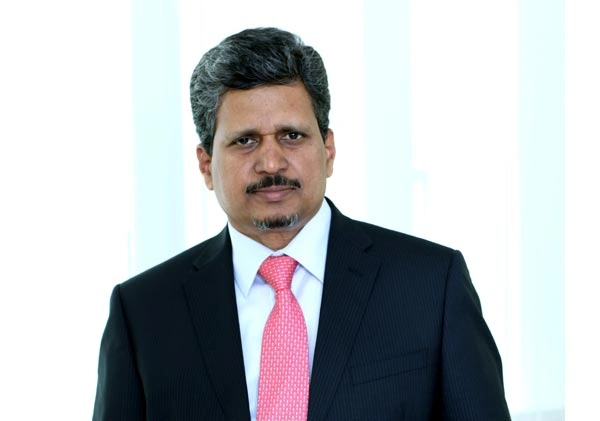
Director General & CEO, Indian Machine Tool Manufacturers’ Association (IMTMA)
The machine tool industry is a key to ‘Make in India’
Product Updates
Explore Latest Welding Products